The 111th Installment
Participation in the "Tsukuba Challenge 2018" Robot Competition
by Tomoyuki Ohkubo,
Assistant Professor, Master Program of Innovation for Design and Engineering
In 2018 I had the opportunity to develop and produce an autonomous mobile robot together with students as part of the Tsukuba Challenge 2018. The great ambition of the nine working students and study abroad students on my team is something that sticks in my memory. Autonomous mobile robots have made headlines in recent years and are expected to find use in numerous fields going forward. I think the Tsukuba Challenge is an important opportunity for acquiring skills in this area for students looking to build a career in the future. I very much hope to participate in the next challenge, which is set for fall, 2019, after further honing my own skills.
Skill contests and tournaments are held in numerous fields as a way to cultivate one's skills and develop young engineers. Naturally, many such events are also held in the field of robotics.
To give a few examples:
- Idea Confrontation / National College of Technology Robot Contest
Nicknamed Tech School Robocon, this popular robot contest is broadcast on NHK and sees participants apply ideas to different problems every year and have their creations compete in events.
- All Japan Micromouse Contest
Micromouse events have participants send robots through mazes to see whose is the smartest and fastest. These robots are referred to as "micromice."
- All Japan Robot-Sumo Tournament
In these events, robot sumo wrestlers engage in a battle of skills and ideas. Appropriately, the event is held at the Ryogoku Kokugikan.
- Intelligent Ground Vehicle Competition (IGVC)
This autonomous mobile vehicle competition is usually held in the U.S., with teams from universities in countries such as the U.S., Canada, Japan, Taiwan, China, and India.
Many other robot contests are held both in Japan and around the world.
The Tsukuba Challenge that we participated in was a skills challenge held in downtown Tsukuba, Ibaraki Prefecture. With an eye to developing a society where people and robots coexist, the event has participants undertake challenges using cutting-edge technologies. Participating teams produce mobile robots the size of a wheelchair and run them through a stretch of a little over 1 km in an urban environment. To get through the outdoor urban environment, the robots pay attention to their external environment, making decisions about traversal (autonomous travel) as they go. They traverse places that people and cars pass through, which is mainly sidewalks, crosswalks, park pathways, and building and shopping mall interiors.
63 teams and 75 robots participated in the 10th trial run, conducted in between June and November, 2018, and the actual run in November. Consisting mostly of research lab teams from universities in Japan but also included individuals, the teams gave presentations at a symposium about what they achieved through the robot development process. Our team, dubbed "Team Ohkubo of the Advanced Institute of Industrial Technology," entered a robot named " SANGIDAI-1." On the day of the actual run, we were unable to start by the prescribed time and were unfortunately given a "Do Not Start. "Nevertheless, we were able to run the robot for about 20 m during a post-run test, create a mobile robot on a very tight three month schedule, and acquire skills and experience for the following year, but most importantly we furthered our ambitions toward robot technologies.
2018 was the first time that any team consisting only of AIIT students developed a robot for Tsukuba Challenge. Looking back on the process of failure, fumbling around, and trial and error, there are four areas we need to address.
1. Team member turnover
AIIT's students are mostly either working or on study abroad programs, and many of our students are committed to finding the time to attend classes. Several team members who were in the Master Program of Innovation for Design and Engineering and had been with us since development started in June left the team due to busy schedules. Master Program of Information Systems Architecture students filled in the gap, giving us nine members by August. We therefore built a robot in effectively three months.
2. Time commitment
The majority of working students take classes at night after working during the day, then create reports and go back to work the next day. As such, they are unable to make time for robot development on weekdays. On Saturdays, they have classes until the evening. Our team therefore only had time for development on Saturdays from evening to late night, as well as on Sundays.
3. Could not take part in the trial run
In the Tsukuba Challenge, teams can gather data locally and do test runs about 10 times between June and November. Although these dates are set on Saturdays, Sundays, and holidays, we were only able to participate three times on Sunday because of classes team members had to take at AIIT on Saturdays and holidays.
4. Lack of experience
The Tsukuba Challenge lets teams build their own docs at the testing site (City Hall parking lot), but everyone has to bring various equipment such as tents and generators, and they have to carry the robots and testing equipment themselves. To run robots on streets outdoors, they need to be sufficiently durable. Also, teams have to control and start up robots within the time given during the actual run. Since this was our first time participating, we had no experience with things like what kind of robot to build or what we would have to do as a team when the run started, and we were unfamiliar with the rules.
To address all of the above, we did the following:
1. Use modules
Designing electrical circuits and mechanical components from scratch takes time and reduces reliability, so for a lot of these things we used modules that we purchased. Doing this added costs and compromised design flexibility, but it allowed us to shorten design time.
2. Open source software
Intelligent control is needed to make robots read the environment and determine their behavior. And since intelligent control is so complex and requires so many calculations, program development takes a lot of effort and time. We were able to reduce development time by using a number of open source software products, which are programs currently available on the Internet. These included the operating system (Ubuntu), robot control middleware (ROS), and the control program based software (ORNE Navigation).
3. Study session with an experienced team
The Kobayashi Laboratory in the Department of Advance Sciences, Faculty of Science and Engineering has taken part in the Tsukuba Challenge several times in the past and achieved the goals it has set. We asked them to hold a study session where they taught us the relevant skills. This sped up development.
4. Rapid prototyping environment
It takes materials and manpower to process parts. We made use of a rapid prototyping environment where we designed the parts using CAD, printed them out with a 3D printer, and purchased preprocessed components.
5. Communication tools
Communication was a challenge because of the high proportion of working students on team, which meant schedules rarely overlapped. We shared information using Slack, Google Drive, and mailing lists, as well as through weekly meetings.
By doing all this, we were able to take part in the Tsukuba Challenge 2018.
Cleaning robots are products that make liberal use of mobile robot technologies, and one could say that autonomous driving technologies for cars are an example of autonomous movement technologies. Autonomous mobile robot technology development holds promise for a great many other fields, as well, including security robots, disability robots, and agriculture robots. I believe participation in the Tsukuba Challenge was a meaningful opportunity to learn skills that AIIT students will need in building and changing careers. I hope to build up my experience and skills further and participate again in 2019. I hope any readers with an interest will join us in developing robots.
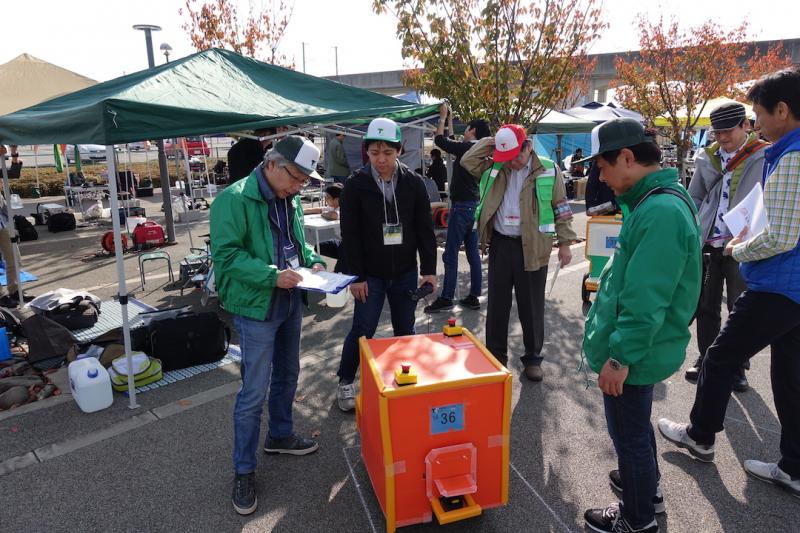
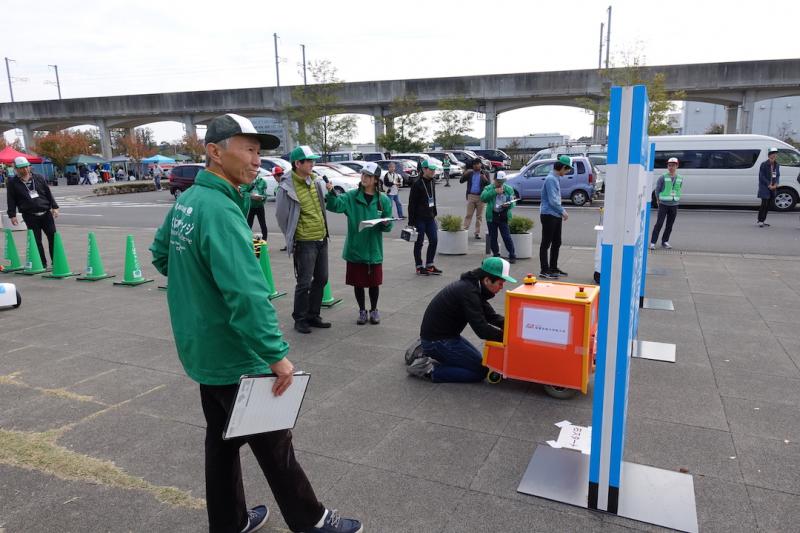
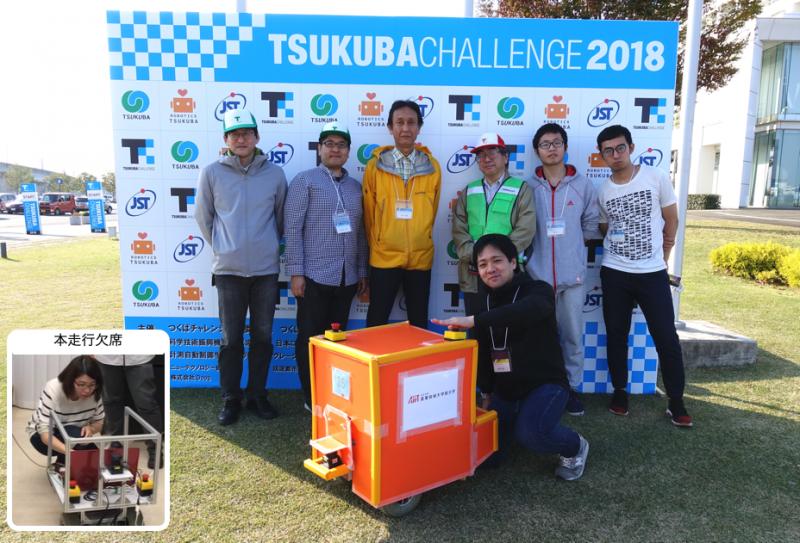